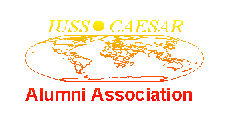
A Russian Discussion of Submarine Gear Noise (Dated But Still Useful)
By Bruce Rule - Mar 2, 2014
PREFACE
Those who may conclude this posting has little practical application should remember statements in my archived article entitled "Philosophically Speaking" that those now on active duty at CUS or elsewhere in the System should do their own research, develop their own resources, i.e., be their own experts.
POSTING
A Russian expert in the field of submarine noise published the following three paragraphs on the site linked below: http://www.fas.org/spp/eprint/snf03221.htm which is worth reading in its entirety.
(Quote) The second generation of Soviet submarines (C,V,Y,D) was less noisy, but progress in decreasing the SSBN signature was achieved by the Soviet shipbuilding industry only during the 1980's with the appearance of the strategic submarine design 667 BDRM (DELTA IV).
During this period, new technologies were introduced which resulted in an order of magnitude improvement in the accuracy of manufacturing gears for the main turbine gear assembly, shafts and propellers. A significant decrease in noise level was also achieved with the application of active noise suppression methods for submarines.
The main reason was that Russia lagged behind the US in manufacturing technologies. In particular, according to specialists' testimony, improving the tolerance for the size of a tooth gear on the submarine's main turbine gear assembly (GTZA) by 0.1 to 0.01 mm permitted a reduction of the submarine's SL by 3-4 orders of magnitude (30-40 dB). (end quote)
COMMENTS:
Those then new manufacturing technologies would have significantly improved the involute profile of the teeth on submarine propulsion system gears. Such improvements would allow smoother contact by opposing teeth and would reduce the irregularities and variations in the surfaces those teeth encountered as motion (power) was/is transferred from the driving gear to the driven gear(s) along the moving “line of action” (contact point) between the teeth thus reducing what can be called “tooth slap” which occurs when the transfer of motion is not continuously smooth because the teeth do not mesh precisely which produces slight variations in transmitted speed and torque.
As gears mesh, the irregular transfer of power produces impact energy. This acoustic energy can be produced by both two-gear, offset systems with single or multiple stages (double reduction) and by coaxial planetary (epicyclic) gear systems which, for a given horsepower, are both space and weight efficient compared to locked-train double reduction gears. As a general rule, coaxial planetary gear systems occupy about one-half the space and have about two-thirds the weight of a double-reduction system that transmits the same power.
Poor (inaccurate) gear cutting techniques that allow excess space to exist between meshing teeth produce not only tooth slap but also can permit the planets to change position - however minuscule - relative to the ring- and sun-gear during each complete revolution of the entire gear system. Planet-gears in a planetary system are held in position by attachment to a common carrier or yoke. In this design, the planets can be allowed to “float” to better achieve load equalization. The positional change the planets experience is either toward the sun-gear or toward the ring-gear within that space created by low-tolerance manufacturing techniques. The angular position between each planet does not change. If there are three planets, the angular separation is 120-degrees; if five planets, the angular separation is 72 degrees. In such systems, the total number of teeth on the ring- and sun-gears must be divisible by an integer. Another numerical relationship useful to know is that the number of teeth on the ring-gear minus the number of teeth on the sun-gear must be divisible by two and that integer quotient is the number of teeth on the planet-gears.
The power input to simple planetary systems in from the sun-gear (usually driven by the main propulsion turbine); the output is from the plant carrier or yoke which directly drives the propeller in a single-stage gear system. In a two-stage system, the output of the first stage is the input to the second-stage.
At relatively high rotational speeds, the planets are held against the ring-gear by centrifugal force but the increased space that can exist between the planets and the sun-gear (in poor tolerance systems) allows more tooth slap to occur, especially during speed changes. At lower speeds – when reduced centrifugal force exists - the planets will, because of gravity, fall away from the ring-gear when they pass through the upper arc of the circle of rotation, and will fall toward the sun-gear. Thus, at low rotational speeds, poorly machined planetary gears can produce impact energy from both tooth slap and positional changes – no matter how small – of the planets relative to the ring- and sun-gears. Thus, these gear systems can produce more noise at very low speeds than at higher speeds.
A useful tutorial on epicyclic (planetary) gearing is available at http://www.uts.com/ResourceCenter/TutorialsandExamples/IntegratedGearSoftware/DesignEpicyclicGearSystems_JimMarsch.pdf
Another useful site:
http://www.gearsolutions.com/article/detail/5837/epicyclic-gearing-a-handbook,