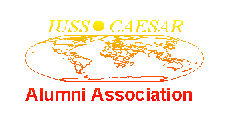
Status of the GTZA OK9VM Main Turbine Gear Assembly During TE Mode Operations
By Bruce Rule - Dec 24, 2015
As already extensively discussed in postings on this site, BOREY Class Russian SSBNs and YASEN Class (NATO: GRANEY) Class Russian SSGNs have “hybrid” propulsion systems: turbine-reduction (TR using the GTZA OK-9VM) for moderate to high speeds, and turbo-electric (TE using the 5,550 hp PG-141 dc motor) for lower speeds, especially below 5-8 knots.
Russian open sources acknowledge submarine main propulsion gear systems have noise (detectability) issues. The TE mode was developed to allow BOREY and YASEN Class units to be less acoustically vulnerable at low speeds and thus more secure, respectively, during missiles patrols, and more effective during ASW search operations.
The term “disabled” has been used to describe the status of the GTZA OK-9VM main turbine and double-reduction planetary gear assembly during TE mode operations. This may be a translation issue because “declutched” would be a more accurate term.
Propulsion turbines that are held in an off-line status but which must be immediately available for high speeds should not be allowed to stop rotating because of very slight deformations – literally sagging – of blades in the stages. To avoid this problem, a motor-driven jacking gear can be placed on the turbine shaft to rotate both the turbine and an integral gear system at ultra-low speeds; one source mentions a five hp motor driving the turbine shaft at 0.1 rpm. Such a mechanism can also be used to ensure uniform cool-down to avoid what is known as “hogging” which occurs when turbine shafts bow upward due to thermal stratification - literally a “hog-back.”
Other issues that could arise during sudden changes from TE to TR mode operations involve the introduction of high volumes of steam to a turbine that has been allowed to cool below normal operating temperatures. Such actions can create severe thermal stresses which could be catastrophic to the turbine. Specific concerns include rotor rupture, blade ductility, sympathetic bearing vibration, and the differential expansion of turbine components such as the main rotor expanding faster than the casing producing what is known as a “rotor-long” condition.
Collectively, these potential issues indicate it is unlikely the BOREY/YASEN GTZA OK-9VM main turbine gear assembly will be allowed to stop rotating during TE mode operations. Further, while ultra-low speeds may address some concerns, a new problem potentially arises because such speeds are not uniform and shafting so-driven may experience sudden slowing and quick accelerations within the ultra-slow speed range. Such events represent noise-producing impacts. And finally, to avoid the above discussed thermo-mechanical stresses that could result from the sudden conversion from TE to high-speed TR mode operations, the GTZA-OK-9VM system may have to be continuously operated at speeds likely to produce the gear-system acoustic vulnerability the hybrid system was developed to avoid.
If the first several BOREY Class SSBNs used not only bow and stern hull sections but also GTZ-OK-9VM main turbine gear assemblies salvaged from several AKUKA Class hulls canceled in the early 1990s, then the above described noise issues could be even more probable.
See the linked site - http://www.iusscaa.org/articles/brucerule/a_russian_discussion_of_submarine_gear_noise_dated_but_still_useful.htm - for discussions noise issues inherent in the design characteristics of planetary gears.